/ Demo case 5: Copper wire production /
ASTA Elektrodraht GmbH manufactures high-quality insulated copper winding material for electrical engineering in the high-energy sector, for instance so-called drill conductors for transformers. The current production process comprises three steps: a) rolling of the material, b) annealing in a gas-fired bell furnace at temperatures between 450 and 600°C (typical cycle is 18-24h), and c) rolling the material to final dimension to reach the required mechanical properties of the product, capable of further processing (enamelling). The target within CITADEL is to merge these three steps into one continuous procedure using a plasma-fired electric furnace. Assuming that the plasma process will be driven by renewable electric energy, natural gas consumption and CO2 emission will be eliminated completely. The overall energy consumption shall be reduced by 30-50%. The nature of plasma treatment through the conductor significantly reduces the temperature gradient along the wire and causes a very uniform grain structure in the material resulting in better electrical and mechanical properties of the final product. Moreover, the plasma treatment improves the surface activation/passivation which increases the performance of the coating process in downstream production.
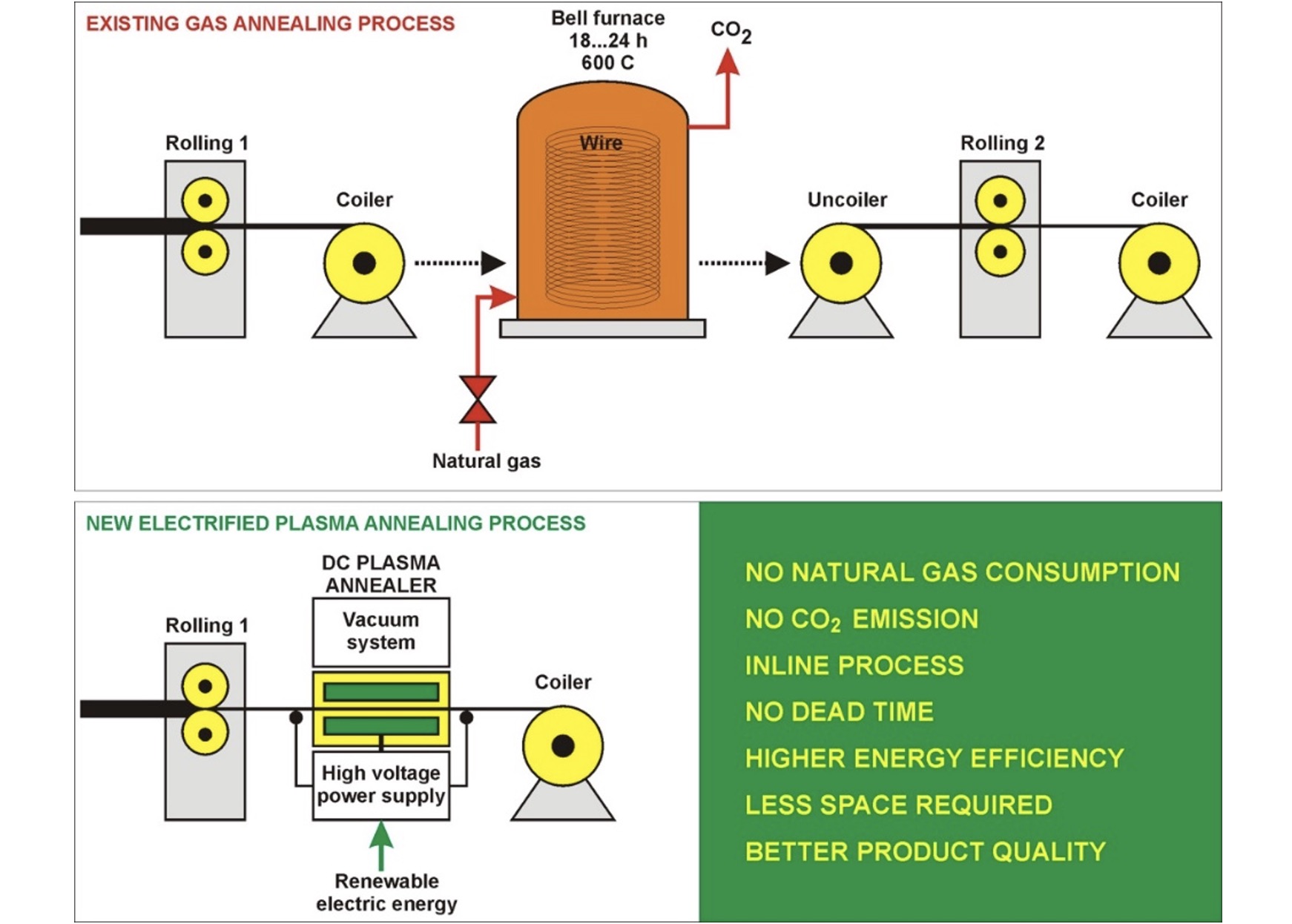
Figure 5: Schematic view showing the process routes for copper wire production: batch gas annealing (top), in-line electric plasma annealing (bottom).