/ Demo case 1: Production of refractory firebricks /
Effectively combating global warming requires a significant reduction in CO2 emissions. This poses enormous challenges, especially for the energy-intensive process and production industry, as this industry accounts for one third of total energy consumption. What is needed is intelligent electrification across all operational processes. Electrification has such a large potential impact on decarbonisation because it allows clean, renewable electricity to power processes that previously used emissions-intensive technologies (such as gas burners). This means that a process that previously produced high emissions can become absolutely emission-free when powered by renewable energy.
Refractory production is one energy intensive sectors of the ceramic industry and depends strongly on fossil fuels for raw materials calcination and sintering, as well as firing of ceramic bonded bricks within a temperature range of 1250 – 1750 ºC. The main product of CERAMICA DEL NALON are fired andalusite bricks, which are indispensable for linings of vessels for steel making and some other industries. Currently, production takes place in a 70m KERABEDARF tunnel kiln with 28 gas burners distributed in 2 combustion zones. The CO2 tonnage produced during combustion of the natural gas going to the atmosphere is roughly half of the brick tonnage being fired. The aim of the CITADEL project is to replace these natural gas burners with electrically operated microwave plasma burners. Using air as heat carrying gas would guarantee 100% CO2 neutral processes.
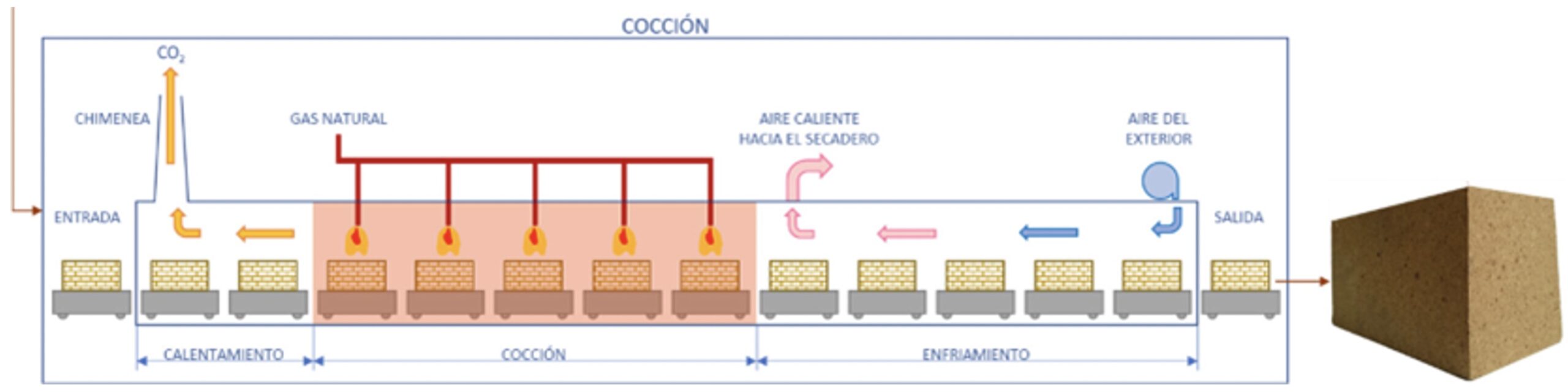
Figure 1: Schematic process of andalusite firebrick production: CITADEL will generate a demonstration process at which the natural gas burner system will be replaced by state of the art electrical powered microwave plasma burners operated with compressed air.
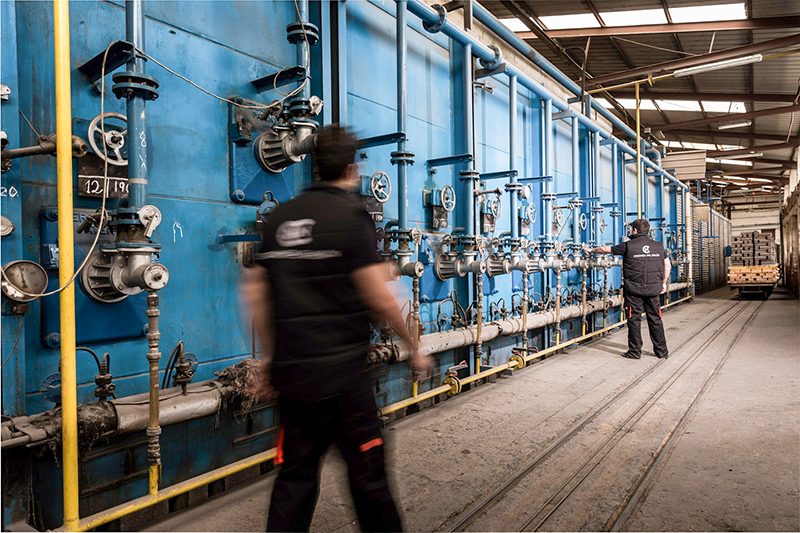
Figure 2: Present KERABEDARF tunnel kiln with 28 gas burners for firing andalusite bricks at 1250°C

Figure 3: Andalusite bricks entering the high temperature zone in the tunnel kiln