/ Demo case 3: Steelmaking /
SIDENOR ACEROS ESPECIALES is leader in the production of special long steel products and medium supplier of bright steel products in the European Market, mainly for the manufacturing of parts and components for the automotive sector, construction and energy. Sidenor is known for its commitment to sustainability and innovation and has implemented a range of measurements to reduce its environmental impact. In line with this path towards sustainability, electrification is a key enabler to process decarbonization with the aim to achieve the ultimate goal of carbon neutrality. Several gas-fired heating processes of Sidenor Process are currently under the focus and among them, ladle and tundish heating procedures are addressed in the frame of CITADEL project.
Ladles and tundishes are vessels used along the steel shop production process to contain the molten steel. In figure 1, it is shown a scheme of Sidenor production route, which is typical for modern European EAF based steel plant, and the process steps where the ladle and tundishes come into play.
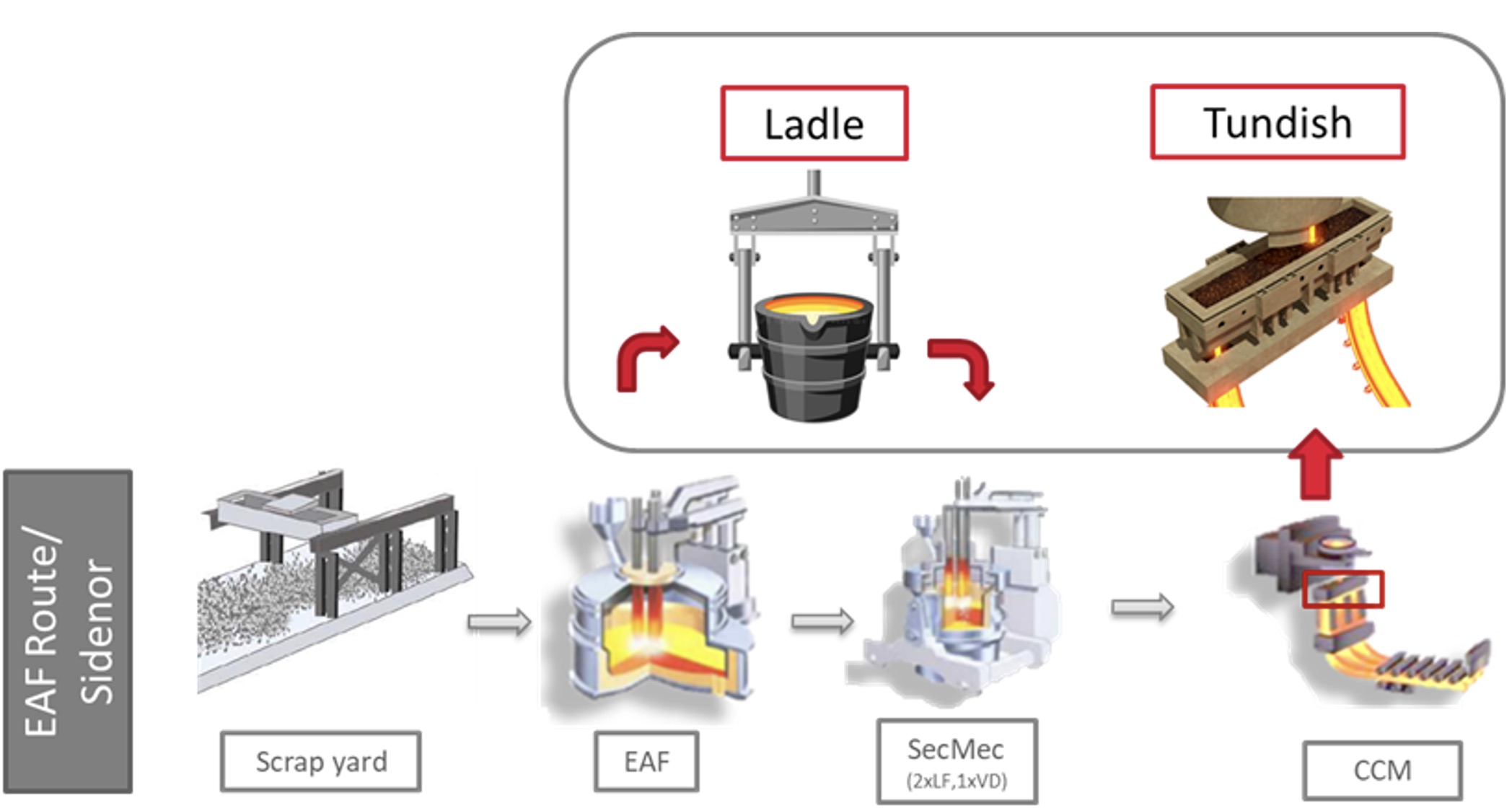
Figure 1: SIDENOR Steel Shop production route, EAF: Electric Arc Furnace, SecMec: Secondary Metallurgy, CCM: Continuous Casting Machine.
A common production procedure in all steel plants is ladle and tundish preheating before filled with liquid steel, with the aim of enabling their refractories to withstand the stringent conditions of the steel production. The most widely implemented method of preheating procedures in steel plants is using heat from gas-air combustion burners. Apart from the high level of CO2 emissions consequence of this process, the main drawback of convectional gas-fired burners is their low thermal efficiency ranging from 5 to 15%. In this frame, CITADEL project will focus on the exploitation of the usage of the O2, by-product of H2 production, to boost the efficiency of ladle preheating with the deployment of oxy-fuel burners. Within the project, currently installed natural gas burners (Figure 2), will be replaced with oxy-fuel burners that will enable the preheating with oxygen instead of air. This change is expected to bring in itself an increase in the efficiency of the preheating processes, a reduction of emissions by about 30% and will permit the transition to hydrogen combustion in the near future.
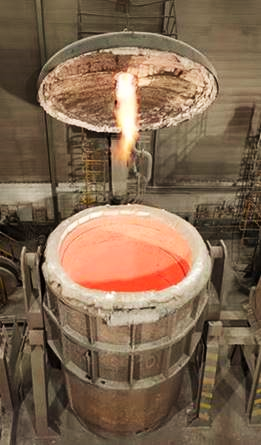
Figure 2: Sidenor Ladle at the preheating station.
On the other hand, to decrease the emissions related to tundish drying and preheating practices, the proposed solution is to replace the current natural gas burners for tundish preheating with an advanced electric resistance-based heating device.